Electric Vehicle Capabilities include testing and analysis of wireless electric vehicle (EV) charging, public EV charging, workplace EV charging, and building energy management systems, which includes residential photovoltaics integration.
The Wireless Charging Lab is used to investigate many topics:
- What are the economic benefits of using electric vehicles for commercial building electrical demand reduction and peak shaving?
- What impact do public charging stations have on building electrical use?
- What methods can be used to eliminate electric utility demand charges for workplace charging stations?
Laboratory projects include:
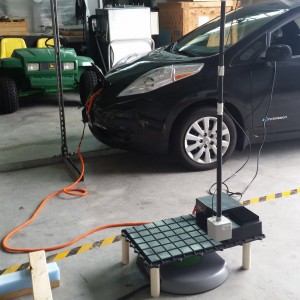
- EV charging and discharging through computer-assisted communication networks
- Operation of a bi-directional vehicle-to-building (V2B) inverter system
- Automated communications system to include the bi-directional charger into a building energy management system
- Using EV traction batteries as distributed energy resources for improving building and utility electric grid efficiency and quality
- Integrating EV battery into a residential PV battery system for extended capacity
- Enhanced EV workplace chargers as part of building energy management system
- Evaluation of wireless chargers
- Wireless charging tests to document testing protocols, evaluate standards, and evaluate operational-related wireless charging characteristics
- Wireless charging products to measure electric and magnetic field emissions according to the Society of Automotive Engineers Technical Information Report Standard J2954 – Wireless Power Transfer for Light-Duty Plug-in / Electric Vehicles and Alignment Methodology
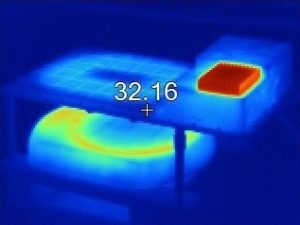
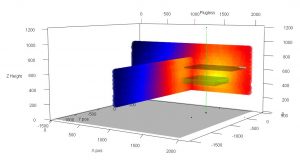
Public Charging Stations
This electric vehicle public charging station was installed in December 2014. Donated by Nissan North America as part of their campaign to provide more public charging stations for their customers, the Signet FC50K-CC 45 kW DC fast charger has two plugs, a CHAdeMO and SAE Combo connector that allows all U.S. PEVs the ability to quick charge if the vehicle is so equipped. Only one vehicle may be actively charged at any given time.
As part of this installation, an AC Level 2 public charging station was also included to provide charging for those vehicles not equipped with fast charging capability. A ChargePoint CT-4021GW single pedestal, dual-plug unit operates at 208 volts with two dedicated 30 amp breakers and provides 6 kW of charging capability per plug. Both of these stations are publicly available and include payment systems that manage the charging session and payment processing.
The public charging stations include payment systems that collect and record the revenue. Charging stations that collect revenue will typically include recurring operating costs for the payment system. The DC fast charger is connected to the Green Lots payment network while the AC Level 2 chargers are connected to the Charge Point network.
These charging stations are monitored for energy consumption and used to determine the impact behind-the-meter installations have on facility electricity bills.
Workplace Charging
The Electric Vehicle Laboratory operates two non-public AC Level 2 charging stations. One is relatively inexpensive to purchase and is manufactured by Clipper Creek. The CS-40 station is equipped with a 30 amp, 208 VAC electrical breaker and a switch closure input that interrupts operation when the contacts are closed. The switch is connected to a low-cost building energy management system (EMS) used to mitigate the impact Plug-in Electric Vehicle (PEV) charging stations may have on building electrical peak demand.
A low-cost AC Level 2 compatible network connected charging station was developed for extending the number of available workplace chargers. This charger has the capability of modulating the current level allowed to each vehicle. Multiple chargers can be connected to a single administration interface. This requires users to login to enable and track energy delivered to each vehicle. The chargers also use the EMS signal to limit power or turn off during peak demand periods. Limiting the current level at each charger can allow more vehicles to charge at the same time. It would not be expected to give each a full charge, but allow employees to recover energy required for daily commute from home to work.
Building Energy Management System
Researchers at the Electric Vehicle Laboratory at the FSEC Energy Research Center developed a simple energy management system (EMS) to help reduce or eliminate the portion of the electric bill associated with charger electrical demand. The focus of the EMS is to minimize facility electricity demand, and maximize workplace charger availability. If EV chargers are not controlled, higher-than-expected utility demand costs can occur. To control these costs, a simple control scheme was developed to regulate the charging station (and even turn it off) before the historical monthly peak demand is exceeded.
The energy management system used to control workplace charging is shown as a Clipper Creek (Switch Enabled) and AeroVironment (SEP 2.0 Enabled). These stations are connected to a dedicated 30 amp single-pole breakers on a 208 VAC electrical service.
AeroVironment
Grid-2-Home modified the AeroVironment (AV) charger to include SEP 2.0 communication capability (bottom left of figure) and this unit is currently in the prototype stage. The SEP client in the charging station wirelessly communicates with the server side of the SEP Gateway that is located inside the facility. The gateway client is then networked to the main SEP server in the building’s computer room. Grid-2-Home also provided a desktop terminal program that can communicate with the main SEP server, to act as a utility company sending demand response commands to the charging station, for example.
Clipper Creek
A less sophisticated system is used to monitor and control the Clipper Creek charging station (bottom center of figure). This charging station employs a switch closure mechanism to disable the charger. An Arduino Yun microprocessor is connected to the Clipper Creek switch closure input via a transistor activated reed relay.
Energy Management System
The Arduino Yun microprocessor monitors the power meter connected to the workplace chargers. A Raspberry Pi microprocessor is also deployed to monitor the facility electric utility meter. In parallel, dedicated data loggers made by Campbell Scientific are also deployed to monitor facility and charging station electrical energy use independently. Each of these microprocessors store collected data in ring format. Finally, an EVSE controller is deployed to monitor the facility power meter data and disable the charging stations when necessary. The main database is located on this server and retains one-minute data over the course of the project. A java script program makes the necessary decisions and sends disable commands either to the SEP server or the Arduino Yun microprocessor to control the workplace chargers.
Residential PV Integration
The Nissan Leaf vehicles used in this project have a DC Fast Charge plug (CHAdeMO) designed to allow quickly charging a vehicle to 80% full charge within 45 minutes. This plug directly connects to the battery which will also allow the discharge of energy. A custom CHAdeMO controller was built to make this connection to a residential battery backed grid connected system. A charge controller was used to interface the EV battery (375 to 400VDC) to the PV system battery (48VDC). The usable PV battery capacity was only 2300Whrs. The EV battery at 42kWhrs provides up to 18 times the capacity.
This system can be operated in grid-connected mode using the EV battery to offset power used from the utility. It also was run in standalone mode with the grid disconnected for extended off grid power. The second vehicle was used as a load during this test, when the source EV battery was low the vehicles were swapped and charged in reverse.
Equipment
The Electric Vehicle Lab, including public and private charging stations, is equipped with:
- Signet FC50K-CC 45 kW DC Level 2 fast charger
- ChargePoint CT-4021GW single pedestal, dual-plug 6 kW AC Level 2 charger
- Princeton Power Systems 30 KVA bi-direction power supply
- Clipper Creek CS-40 6 kW AC Level 2 charger with switch closure operation interrupt
- AeroVironment SEP-2.0 prototype 6 kW AC Level 2 charger with network modulating control
- Two Nissan Leaf electric vehicles
- Plugless 3 kW wireless charger
Previous Vehicle Projects
The Electric Vehicle Transportation Center is a University Transportation Center supported by the U.S. Department of Transportation and is a research and education effort to help create the nation’s electric-vehicle transportation network. The EVTC R&D agenda is comprised of 21 individual projects and their respective teams that conduct the detailed research. A summary of results for each project may be found at EVTC Research.
Additional related research includes:
- Performance monitoring of converted pickup trucks
- Hybrid truck with electric drive and CNG generator
- LED tail lights and turn signals for electric vehicles
- Performance monitoring of electric bus fleet in Miami Beach
[ Last updated: 7/22/2021 ]